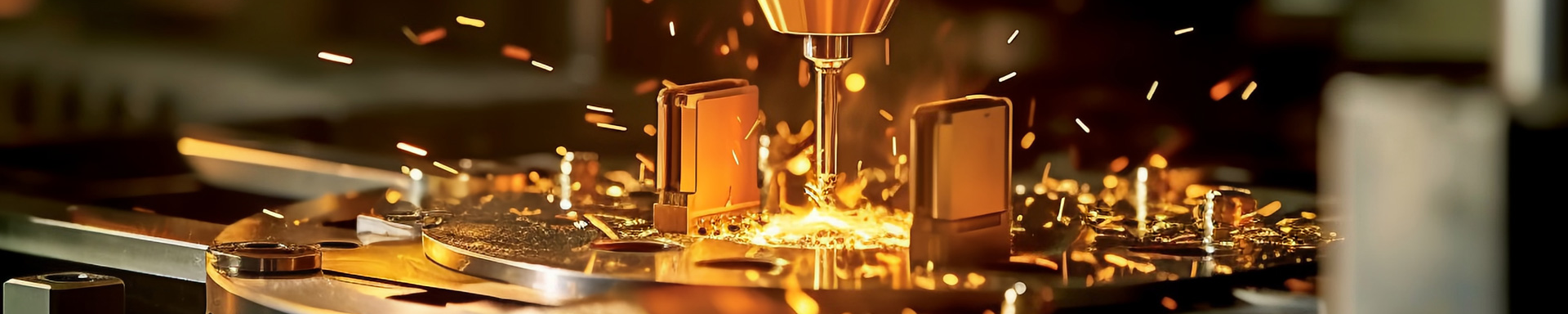
Tecniche avanzate nei processi di pressofusione di automobili
2024-11-22 15:41Miglioramenti della pressofusione ad alta pressione (HPDC)
La pressofusione ad alta pressione (HPDC) rimane una pietra angolare della produzione di componenti per l'automotive, apprezzata per la sua velocità e capacità di creare parti complesse. Tuttavia, la tradizionale HPDC spesso ha difficoltà a ottenere una precisione dimensionale e una qualità superficiale coerenti su grandi lotti. I miglioramenti moderni si concentrano sull'ottimizzazione dell'intero processo, dalla progettazione dello stampo e dalla selezione dei materiali ai parametri di iniezione e alle tecniche di post-elaborazione. Ciò include progressi nei materiali dello stampo che offrono una resistenza all'usura superiore e proprietà di trasferimento del calore, portando a una maggiore durata dello stampo e a una migliore qualità delle parti. Inoltre, l'implementazione di sofisticati sistemi di controllo consente un monitoraggio e una regolazione precisi di parametri come pressione di iniezione, velocità e tempo di mantenimento, riducendo al minimo le variazioni e garantendo risultati coerenti.
Un'altra area critica di miglioramento è l'uso di software di simulazione. Questi programmi avanzati consentono agli ingegneri di testare virtualmente vari progetti di stampi e parametri di iniezione prima che inizi la produzione effettiva. Questa capacità predittiva riduce significativamente la necessità di costose prototipazioni fisiche e iterazioni, accelerando il processo di sviluppo e riducendo al minimo gli sprechi. L'integrazione di sensori sofisticati all'interno della macchina per pressofusione fornisce feedback in tempo reale, migliorando ulteriormente il controllo del processo e ottimizzando il risultato. Questo approccio basato sui dati porta a miglioramenti significativi nella qualità delle parti, riducendo i difetti e aumentando l'efficienza complessiva.
Fusione a parete sottile
La domanda di veicoli leggeri sta spingendo fortemente verso la pressofusione a parete sottile. Questa tecnica consente la creazione di componenti con spessori di parete notevolmente ridotti, mantenendo al contempo l'integrità strutturale. Ciò non solo contribuisce alla riduzione del peso, ma riduce anche i costi dei materiali. Tuttavia, ottenere una fusione a parete sottile richiede un controllo preciso sul processo di iniezione e l'uso di stampi specializzati. Le tecniche avanzate impiegano design di stampi ottimizzati con sistemi di raffreddamento migliorati per garantire una rapida solidificazione e prevenire difetti come porosità o deformazione. Lo sviluppo di leghe di alluminio ad alta resistenza specificamente adatte per applicazioni a parete sottile migliora ulteriormente la fattibilità e la resistenza di questi componenti.
Il processo trae vantaggio anche dalle innovazioni nella progettazione degli stampi, incorporando caratteristiche come sistemi di gating ottimizzati e strategie di sfiato per migliorare il flusso del metallo e ridurre al minimo l'intrappolamento dell'aria. Le simulazioni avanzate svolgono un ruolo cruciale nel prevedere potenziali problemi e ottimizzare i parametri di processo per ottenere la geometria a parete sottile desiderata mantenendo al contempo l'integrità strutturale e la qualità della superficie. L'implementazione di sistemi di monitoraggio e controllo in tempo reale riduce ulteriormente i difetti e garantisce una produzione costante di componenti di alta qualità.
Pressofusione multi-materiale
L'integrazione di più materiali all'interno di un singolo componente pressofuso apre interessanti possibilità per migliorare funzionalità e prestazioni. Questo approccio consente la combinazione di materiali con proprietà diverse, come resistenza, conduttività termica e conduttività elettrica, all'interno di un singolo componente. Ad esempio, un componente potrebbe incorporare un'anima in lega di alluminio ad alta resistenza per l'integrità strutturale, combinata con un materiale più morbido e duttile in aree specifiche per migliorare la funzionalità o ridurre l'usura. Ciò richiede una progettazione sofisticata dello stampo e un controllo preciso sul processo di iniezione per garantire un posizionamento e un legame accurati dei diversi materiali.
Le tecniche avanzate nella pressofusione multi-materiale spesso comportano l'uso di inserti specializzati all'interno dello stampo per definire i confini di materiali diversi. Un controllo preciso sui parametri di iniezione è fondamentale per prevenire la miscelazione o la delaminazione dei diversi materiali. L'uso di software di simulazione è particolarmente critico nell'ottimizzazione dei parametri di progettazione e di processo, assicurando l'integrazione e l'incollaggio di successo di più materiali all'interno del componente finale. Anche lo sviluppo di nuove tecniche di giunzione, come la saldatura a frizione o la saldatura per diffusione, sta svolgendo un ruolo importante nella creazione di fusioni multi-materiale robuste e affidabili.
Materiali e rivestimenti avanzati per stampi
Le prestazioni e la longevità degli stampi per pressofusione hanno un impatto significativo sull'efficienza complessiva e sulla qualità del processo. I materiali tradizionali per stampi, pur essendo funzionali, spesso presentano limitazioni in termini di resistenza all'usura, conduttività termica e resistenza alla corrosione. I progressi moderni si concentrano sullo sviluppo e l'applicazione di materiali innovativi per stampi, come leghe di acciaio avanzate, compositi ceramici e nuovi rivestimenti. Questi materiali offrono una maggiore durata, consentendo tassi di produzione più elevati e una maggiore durata degli stampi.
Rivestimenti specializzati, applicati alla superficie dello stampo, migliorano ulteriormente la resistenza all'usura, riducono l'attrito e migliorano la finitura superficiale dei componenti fusi. Questi rivestimenti possono essere adattati ad applicazioni specifiche, offrendo proprietà personalizzate come caratteristiche di trasferimento termico o rilascio migliorate. Lo sviluppo di rivestimenti più durevoli e affidabili è in corso, con un'attenzione rivolta al raggiungimento di una resistenza all'usura ancora maggiore e al miglioramento della qualità complessiva delle parti fuse. Ciò consente tassi di produzione aumentati e una migliore qualità dei componenti, riducendo al minimo i tempi di fermo associati alla manutenzione e alla sostituzione dello stampo.